How is pressure-velocity compounding accomplished?
Answers:
It is a combination of pressure compounding and velocity compounding. Steam is expanded partially in a row of nozzles whereupon its velocity gets increased. This high velocity steam then enters a few rows of velocity compounding whereupon its velocity gets successively reduced. (Fig. 5) The velocity of the steam is again increased in the subsequent row of nozzles and then again it is allowed to pass onto another set of velocity compounding that brings about a stage-wise reduction of velocity of the steam. This system is continued. How is the washing of turbine blades carried out with the condensate?
Answers: 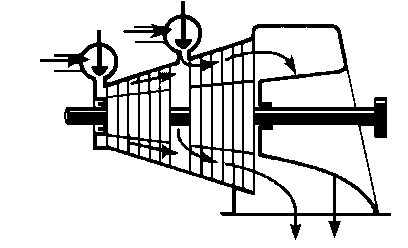
- The washing is carried out with the condensate at 100°C.
- The turbine is cooled or heated up to 100°C and filled with the condensate via a turbine drain.
- The rotor is turned or barred by hand and the condensate is drained after 2 to 4 hours.
- It is then again filled with the condensate at 100°C (but up to the rotor center-level), the rotor is rotated and the condensate is drained after sometime. This process is repeated several times.
How is turbine blade washing with wet steam carried out?
Answers:
- Wet steam produced usually by injecting cold condensate into the superheated steam, is introduced to the turbine which is kept on running at about 20% of nominal speed.
- For backpressure turbine the exhaust steam is let out into the open air through a gate valve. For a condensing turbine, the vacuum pump is kept out of service while cooling water is running, with the effect that the entering cooling steam is condensed. The condensate is drained off.
- The washing steam condition is gradually adjusted to a final wetness of 0.9 to 0.95.
Note, it is important:
- not to change washing steam temperature by 10°C/min,
- to keep all turbine cylinder drains open.
How is velocity compounding accomplished?
Answers:
- This is accomplished by an arrangement with alternate rows of fixed blades and moving blades. The mounted on the casing while the moving blades are keyed in series on a common shaft. The function of the fixed blades is to correct the direction of entry of steam to the next row of moving blades.
- The high velocity steam leaving the nozzles passes on to the 1st row of moving blades where it suffers a partial velocity drop.
- Its direction is then corrected by the next row of fixed blades and then it enters the 2nd row of moving blades. Here the steam velocity is again partially reduced. Since only part of the velocity of the steam is used up in each row of the moving blades, a slower turbine results. This is how velocity compounding works.
How many governors are needed for safe turbine operation? Why?
Answer: Two independent governors are needed for safe turbine operation:
- One is an over speed or emergency trip that shuts off the steam at 10 percent above running speed (maximum speed).
- The second, or main governor, usually controls speed at a constant rate; however, many applications have variable speed control.
How many types of particle-impact damage occur in turbine blades?
Answers:
- Erosion/corrosion.
- Foreign-particle impacts.
- Solid-particle erosion.
- Water damage.
How to prevent turbine deposition?
Answers:
By upgrading the quality of steam. That is by ensuring proper:
- Boiler feed water quality.
- Steam boiler model.
- Boiler design.
- Boiler operation.
How will you detect that misalignment is the probable cause of excessive vibration?
Answers:
- Coupling to the driven machine is to be disconnected.
- The turbine is to be run alone.
- If the turbine runs smoothly, either misalignment, worn coupling or the driven equipment is the cause of the trouble.
How would you slop a leaky tube in a condenser that was contaminating the feed-water?
Answer: To stop a leaky tube from contaminating the feed water, shut down, remove the water-box covers, and fill the steam space with water. By observing the tube ends you can find the leaky tube. An alternate method is to put a few pounds of air pressure in the steam space, flood the water boxes to the top inspection plate, and observe any air bubbles. Once you have found the leaky tube, drive a tapered bronze plug (coated with white lead) into each end of the tube to cut it out of service. This allows you to use the condenser since the tubes need not be renewed until about 10 percent of the tubes are plugged.
How would you stop air from leaking into a condenser?
Answer: First, find the leak by passing a flame over the suspected part while the condenser is under vacuum. Leaks in the flange joints or porous castings can be stopped with asphalt paint or shellac. Tallow or heavy grease will stop leaks around the valve stems. Small leaks around the porous castings, flange nuts, or valve stems can always be found by the flame test. So, you might have to put the condenser under a few pounds of air pressure and apply soapsuds to the suspected trouble parts.
In how many patterns are tie wires used?
Answers:
- In one design, tie wire is passed through the blade vane.
- In another design, an integral stub is jointed by welding/brazing.
In steam turbines, is there any alternative to the shrunk-on-disc design?
Answers:
Two designs are available at present:
- Welded rotor in which each individual disc is welded, instead of shrunk, onto the main shaft.
- Monobloc rotor in which the entire shaft and blade assembly is manufactured from a single forging.
In which case does upgrading imply life extension of steam turbines?
Answer: For a capital-short electric utility plant, upgrading comes to mean extending the life of that plant scheduled for retirement.
In which cases does erosion corrosion damage appear?
Answer: It is commonly encountered in nuclear steam turbines and old fossil-fuel-fired units that employ lower steam temperatures and pressures.
In which cases does moisture-impingement and washing erosion occur?
Answers:
- These are encountered in the wet sections of the steam turbine.
- For nuclear power plants, these wet sections can involve parts of high-pressure cylinder.
In which cases does upgrading mean up-rating the turbine capacity?
Answer: For an electric utility system facing uncertain load growth, upgrading is chiefly up-rating. It is an inexpensive way to add capacity in small increments.
In which part of the steam turbine does corrosion fatigue occur?
Answer: In the wet stages of the LP cylinder.
In which part of the steam turbine does stress corrosion cracking (SCC) occur?
Answer: In the wet stages of the low-pressure turbine.
In which section of the steam-turbine rotors is the problem of rotor failure mostly prevalent?
Answers: Rotor failures occur mostly on the large low-pressure rotors.
What are the basic causes of the problems are?
Answers:
- Normal wear.
- Fatigue failure due to high stress.
- Design deficiency.
- Aggressive operating environment
In which turbine is this pressure compounding used?
Answer: In the Rateau turbine.