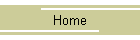

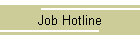
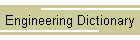
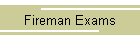
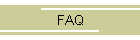
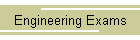
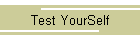

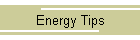
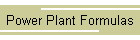
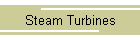
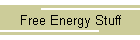
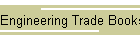
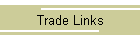
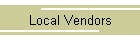
| |
In which turbine is tip leakage a problem?
Answer: Tip leakage is a problem in reaction turbines. Here, each vane forms a nozzle; steam must how through the moving nozzle to the fixed nozzle. Steam escaping across the tips of the blades represents a loss of work. Therefore, tip seals are used to prevent this. In which turbine is velocity compounding utilized? Answer: In the Curtis turbine. In which turbines, is this pressure-velocity compounding principle employed? 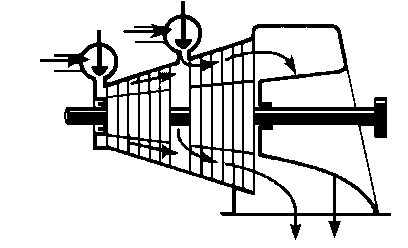 Answer: In the Curtis turbine. In which zone of steam turbines has temperature-creep rupture been observed? Answer: Damage due to creep is encountered in high temperature (exceeding 455°C) zones. That is, it has been found to occur in the control stages of the high-pressure and intermediate-pressure turbines where steam temperature sometimes exceed 540°C. In the reheat stage, it has been observed that creep has caused complete lifting of the blade shroud bands. Is there any adverse effect off full-arc admission operation? Answer: At low loads, this results in a heat-rate penalty, due to throttling over the admission valves. Is there any alternative to the shrunk-on-disc design? Answers: Two designs are available at present: - Welded rotor in which each individual discs are welded, instead of shrunk, onto the main shaft.
- Monobloc rotor in which the entire shaft and blade assembly is manufactured from a single forging.
Is there any factor other than corrodents and erodents that contributes to turbine blade failure? Answers: Turbine blade damage and failures can be effected by vibration and fatigue. - These arise due to flow irregularities introduced because of manufacturing defects, e.g. lack of control over tolerances.
- System operating parameter, e.g. low flow may excite various modes of vibration in the blades.
Is there any other type of racking occurring in HP/IP rotors and causing rotor failures? Answers: - Blade-groove-wall cracking.
- Rotor-surface cracking.
Of all the factors that contribute to the unreliability of steam turbines, which one is the most prominent? Answer: It is the problem of turbine blade failures that chiefly contribute to the unreliability of steam turbines. Rim cracking continues to be a problem of shrunk-on-disc type rotors in utility steam turbines. Where does it occur? Answer: Cracking has been located at the outer corners of tile grooves where the blade root attaches to the rotor. So can you recommend this technique as a permanent measure? Answer: No, this can be recommended in extreme cases or at best temporarily. So what should be the more sound approach? Answers: - The more reasonable and better approach is to replace the damaged blades with new ones that are stiffened by:
- Serrating the interface surface of individual blades so they interlock, or
- Welding the blades together.
- In some cases, a single monolithic block is machined out to manufacture the blades in a group.
- In some other cases, blades themselves are directly welded into the rotor.
Steam blowing from a turbine gland is wasteful. Why else should it be avoided? Answer: It should be avoided because the steam usually blows into the bearing, destroying the lube oil in the main bearing. Steam blowing from a turbine gland also creates condensate, causing undue moisture in plant equipment. The consequences of turbine depositions have three effects? Answers: - Economic Effect:
- Reduction in turbine output
- Decrease in efficiency requiring higher steam consumption.
- Effect of Overloading and Decreasing Reliability in Operation:
- Pressure characteristic in the turbine gets disturbed with the effect that thrust and overloading of thrust bearing increase.
- Blades are subjected to higher bending stresses.
- Natural vibrations of the blading are affected.
- Vibration due to uneven deposition on turbine blading.
- Valve jamming due to deposits on valve stems.
- Corrosion Effect:
- Fatigue corrosion.
- Pitting corrosion.
- Stress corrosion.
Usually it has been found that SCC attack takes place particularly at keyways of shrunk-on-disc rotors of low-pressure turbines. Why are keyways prone to SCC attack? Answers: - Keyways shrunk-fit each disc onto tile rotor shaft. They improve the rigidity of the connection between the disc and the central shaft However, key ways are subjected to abnormal centrifugal forces due to high overspeed, that reduce the amount of shrink. Tangential stresses tend to gravitate at the keyway connection and steam tends to condense.
- It is a one-piece-construction, and thus has inherent rigidity.
- Advanced steel making techniques enable building of monobloc rotors almost free from non-metallic inclusions and gas bubbles. Even large monobloc rotors of clean steel are being manufactured today.
- It exhibits lower inherent stresses.
- The chance of disc loosening during operation is eliminated.
- Highly stressed keyway is eliminated.
What are four types of thrust bearings? Answers: - babbitt-faced collar bearings
- tilting pivotal pads
- tapered land bearings
- rolling-contact (roller or ball) bearings
What are four types of turbine seals? Answer: - Carbon rings fitted in segments around the shaft and held together by garter or retainer springs.
- Labyrinths mated with shaft serrations or shaft seal strips.
- Water seals where a shaft runner acts as a pump to create a ring of water around the shaft. Use only treated water to avoid shaft pitting.
- Stuffing box using woven or soft packing rings that are compressed with a gland to prevent leakage along the shaft.
What are some common troubles in surface-condenser operation? Answer: The greatest headache to the operator is loss of vacuum caused by air leaking into the surface condenser through the joints or packing glands. Another trouble spot is cooling water leaking into the steam space through the ends of the tubes or through tiny holes in the tubes. The tubes may also become plugged with mud, shells, debris, slime, or algae, thus cutting down on the cooling-water supply, or the tubes may get coated with lube oil from the reciprocating machinery. Corrosion and dezincification of the tube metal are common surface-condenser troubles. Corrosion may be uniform, or it may occur in small holes or pits. Dezincification changes the nature of the metal and causes it to become brittle and weak. What are the advantages of steam turbines over reciprocating steam engines? Answers: - Steam turbine has higher thermal efficiency than reciprocating steam engines.
- The brake horsepower of steam turbines can range from a few HP to several hundred thousand HP in single units. Hence they are quite suitable for large thermal power stations.
- Unlike reciprocating engines, the turbines do not need any flywheel, as the power delivered by the turbine is uniform.
- Steam turbines are perfectly balanced and hence present minimum vibrational problem.
- High rpm l8000 - 24000 can be developed in steam turbines but such a high speed generation is not possible in the case of reciprocating steam engines.
- Some amount of input energy of steam is lost as the reciprocating motion of the piston is converted to circular motion.
- Unlike reciprocating steam engines, no internal lubrication is required for steam turbines due to the absence of rubbing parts.
- Steam turbines, if well designed and properly maintained, are more reliable and durable prime movers than steam engines.
What are the advantages of velocity compounding? Answers: - The velocity compounding system is easy to operate and operation is more reliable.
- Only two or three stages are required. Therefore, first cost is less.
- Since the total pressure drop takes place only in nozzles and not in the blades, the turbine casing need not be heavily built. Hence the economy in material and money.
- Less floor space is required.
What are the advantages of welded rotors? Answers: - Welded rotor is a composed body built up by welding the individual segments. So the limitations on forgings capacity do not apply.
- Welding discs together results in a lower stress level. Therefore, more ductile materials can be chosen to resist SCC attack.
- There are no keyways. So regions of high stress concentrations are eliminated.
What are the basic causes of the problem of rotor failure? Answers: - Normal wear.
- Fatigue failure due to high stress.
- Design deficiency.
- Aggressive operating environment
What are the causes of radial axial-bore cracks on HP/IP rotors/shafts? Answers: - The predominant cause is creep, which may act with or without low cycle fatigue.
- Also the cracks result due to poor creep ductility due to faulty heat treatment process.
What are the differences between impulse and reaction turbines? Answers: - The impulse turbine is characterized by the fact that it requires nozzles and that the pressure drop of steam takes place in the nozzles.
- The reaction turbine, unlike the impulse turbines has no nozzles, as such. It consists of a row of blades mounted on a drum. The drum blades are separated by rows of fixed blades mounted in the turbine casing. These fixed blades serve as nozzles as well as the means of correcting the direction of steam onto the moving blades.
- In the case of reaction turbines, the pressure drop of steam takes place over the blades. This pressure drop produces a reaction and hence cause the motion of the rotor.
What are the disadvantages of velocity compounding? Answers: - Steam velocity is too high and that is responsible for appreciable friction losses.
- Blade efficiency decreases with the increase of the number of stages.
- With the increase of the number of rows, the power developed in successive rows of blade decreases. For as much as, the same space and material are required for each stage, it means, therefore, that all stages are not economically efficient.
What are the factors that contribute to bearing failure in a steam turbine? Answers: - Improper lubrication.
Only the recommended lubricant should be used. - Inadequate water-cooling.
- The jacket temperature should be maintained in the range of 37-60°C
- The flow of cooling water should be adjusted accordingly.
- Misalignment.
It is desirable that ball bearings should fit on the turbine shaft with a light press fit. If the fitting is too tight, it will cause cramping. On the other hand, if the fitting is too loose it will cause the inner race to turn on the shaft. Both conditions are undesirable. They result in wear, excessive vibration and overheating. And bearing failure becomes the ultimate result. - Bearing fit.
- Excessive thrust.
- Unbalance.
- Rusting of bearing.
Goto Page 6 Question & Answers Steam Turbines www.massenginers.com | | |